Penetrant Testing
This is a simple low-cost method of detecting surface-breaking flaws such as cracks, laps, porosity, etc. To be detected, the flaw must reach the surface to be tested.
Penetrant testing is one step up from visual inspection and offers many advantages, such as speed, large-area coverage.
The article addresses a step by step dye Penetrant testing process. There are two techniques for dye Penetrant test as follow:
- Color contrast or visible dye Penetrant testing
- Fluorescent dye Penetrant testing
- Each of above techniques can be performed with three different processes as follow:
- Solvent Removable
- Water Washable
- Hydrophilic emulsification
In this article, we are going to explain the simplest technique and process which is used for portable application in the field. Some of the above-mentioned processes are designed for lab test application and would not be easy to be conducted in the field. Here is the step by step dye Penetrant testing process:
-
Step 1 – Pre cleaning of the Surface
The 3 spray cans (aerosol) are provided for this test. First one is named cleaner. The technician sprays the cleaner to the test object and then cleans the surface with non-used rag or cloth. The sprayed material is evaporated rapidly. So the technician needs to clean the surface instantly. -
Step 2- Application of Penetrant (dipping, spray, brush)
In the second step, the technician applies Penetrant spray can to the surface which is in sharp red color. The technician needs to wait for 5 to 15 minutes depends on test procedure. In this time, the Penetrant liquid enters to the crack (normally is not visible). The Penetrant liquid soaks inside of the defects/ imperfections by capillary action. -
Step 3- Removal of the Excess Penetrant Liquid
In the third step, the technician removes Penetrant liquid from the surface by rag or cloth and uses back and forth rubbing to clean the surface. No red color should be visible after cleaning. Then technician takes a clean rag and sprays some cleaner on a cloth and then cleans the surface one more time. This can be done two or three times to remove all Penetrant liquid from the surface. Please note by the capillary action; the Penetrant liquid still is in the cracks or hot tear or any other imperfection. It will not come out by cleaning as described. -
Step 4 - Application of Developer
In the fourth step, the technician takes the developer spray can and agitates it and then sprays to the surface. Then he waits for 10 minutes. In this time, the defect will be visible, the developer material uses reverse capillary action and bleeds out the red Penetrant, and if there is a crack in the surface, you will see a red line within the white color covered by developer material. -
Step 5 - inspection of test surface
In the fifth step, The ASNT Level II liquid Penetrant inspector evaluates the test result based on the acceptance criteria indicated in the approved test procedure. Please note one indication might be considered imperfection and be rejected by one acceptance criteria and be accepted by another one. So it is imperative that the test be evaluated with right acceptance criteria. -
Step 6 - Liquid Penetrant Test Report
In the sixth step, The technician prepares the report and indicates the test results and submits to the customer.
- The choice of technique for any specific application is based on:
- The surface finish of the specimen
- The compatibility of the materials with the specimen
- The sensitivity required
- The size, shape and accessibility of the area to be inspected
- The ultimate use of the component.
Fluorescent Penetrant are usually used when the maximum flaw sensitivity is required.
The principle of liquid Penetrant testing is that the liquid Penetrant is drawn into the surface-breaking crack by capillary action and excess surface Penetrant is then removed; a developer (typically a dry powder) is then applied to the surface, to draw out the Penetrant in the crack and produce a surface indication. Cracks as narrow as 150 nanometers can be detected. The indications produced are much broader than the actual flaw and are therefore more easily visible.
Liquid Penetrant testing can be applied to any non-porous clean material, metallic or non-metallic, but is unsuitable for dirty or very rough surfaces. Surface cleaning is a vital part of the Penetrant testing technique. The method can be manual, semi-automatic or fully automated. Penetrant inspection, continuous-operation production lines in which the specimens are cleaned, dipped, washed, dried, etc on a time cycle are common.
Recently, equipment to fully automate the visual inspection stage of the process, by robotic handling of the specimen on a programmed procedure with television camera viewing and pattern recognition to identify and recognize flaws, has been introduced. Television image enhancement processes can be included.
A special, very high sensitivity Penetrant process, using radioactive tracers is sometimes used, but requires very stringent safety procedures.
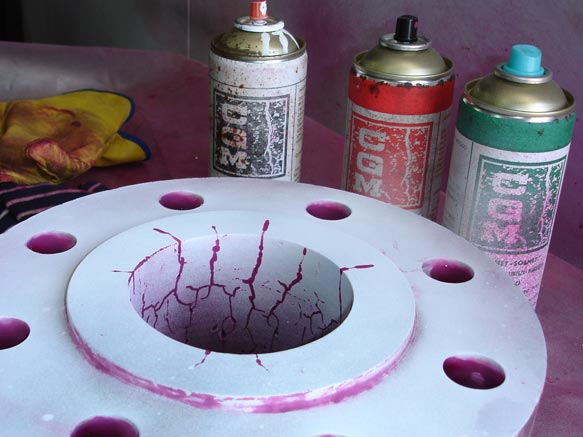
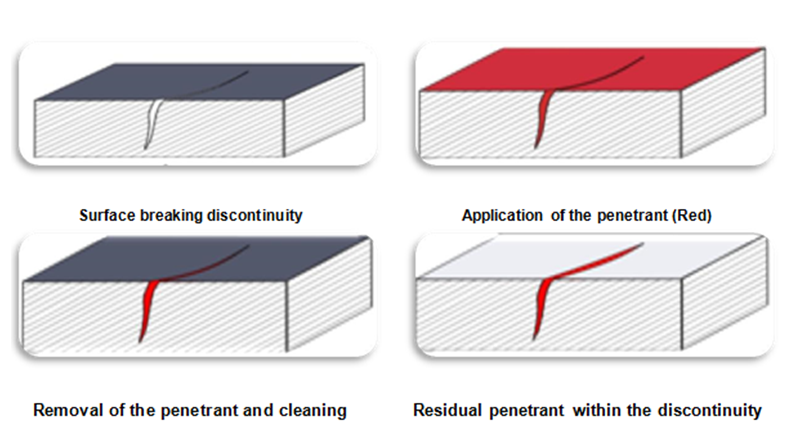
Hardness testing
The application of hardness testing enables you to evaluate a material’s properties, such as strength, materials amenability and wear resistance, and so helps you determine whether a material or material treatment is suitable for the purpose you require.
HOW DO HARDNESS TEST WORK?
A hardness test is usually performed by pressing a specifically dimensioned and loaded object (indenter) into the surface of the fabric you’re testing. The hardness is decided by measuring the depth of indenter penetration or by measuring the dimensions of the impression left by an indenter. Hardness tests that measure the depth of indenter penetration include: Rockwell, Instrumented Indentation Testing, and Ball Indentation Hardness Hardness tests that measure the dimensions of the impression left by the indenter include: Vickers, Knoop, and Brinell
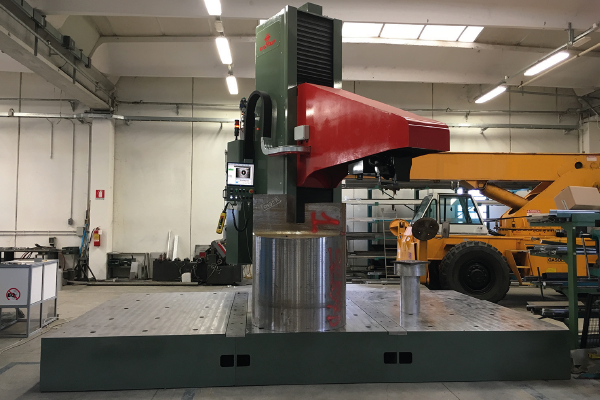