Eddy Current Testing
Eddy currents are a manifestation of electromagnetic induction occurring when a magnetic field is applied to a conductor. If the magnetic induction Β in a material changes with time, a voltage is generated in the material, according to the equation – dB/dt = V/A
where b = Magnetic flux density, V = voltage and A = cross section of enclosed area normal to the lines of magnetic flux, m 2 . This is known as faraday’s law of magnetic induction.
Eddy current array (ECA) is a nondestructive testing technology that provides the ability to electronically drive multiple eddy current coils, which are placed side by side in the same probe assembly. Each individual eddy current coil in the probe produces a signal relative to the phase and amplitude of the structure below it. This data is referenced to an encoded position and time and represented graphically as a C-scan image. Most conventional eddy current flaw detection techniques can be reproduced with ECA inspections; however, the remarkable advantages of ECA technology allow improved inspection capabilities and significant time savings.
ECA technology includes the following advantages:
- A larger area can be scanned in a single-probe pass, while maintaining a high resolution.
- Less need for complex robotics to move the probe; a simple manual scan is often enough.
- C-scan imaging improves flaw detection and sizing.
- Complex shapes can be inspected using probes customized to the profile of the part being inspected.
The strength of the eddy currents produced depends on the:
- Electrical conductivity of the specimen
- Magnetic permeability (for a ferromagnetic specimen)
- Stand-off distance between the specimen and coil
- AC frequency used in the exciting coil
- Dimensions of the coil and specimen
Eddy current (EC) testing is a no contact method for the inspection of metallic parts. Eddy currents are fields of alternating magnetic current that are created when an alternating electric current is passed through one or more coils in a probe assembly. When the probe is linked with the part under inspection, the alternating magnetic field induces eddy currents in the test part. Discontinuities or property variations in the test part change the flow of the eddy current and are detected by the probe in order to make material thickness measurements or to detect defects such as cracks and corrosion.
Over the years, probe technology and data processing have advanced to the point where eddy current testing is recognized as being fast, simple, and accurate. The technology is now widely used in the aerospace, automotive, petrochemical, and power generation industries for the detection of surface or near-surface defects in materials such as aluminum, stainless steel, copper, titanium, brass, Inconel, and even carbon steel (surface defects only).
Eddy Current Works :
The drawings below represents schematically how does eddy current works. The coil causes a magnetic field, which initiate eddy current. If a defect appears in the effective area, the eddy current have to take a different way, this changes the impedance of the coil and the operator see the changes on his screen.
EDDY CURRENT STANDS FOR :
High testing speed, no blank surface needed, no danger to the environment, painted surfaces have no influence, no temperature influence, evaluation of crack depth.
PIPE INSPECTION OF HEAT EXCHANGERS
Various materials could be checked, like carbon steel, stainless steel, duplex, alloy or other conductive materials.
SURFACE CRACK INSPECTION
The cracks below could be found by eddy current. Special probes allow to detect inside cracks from outside, depending on the material and wall thickness. Even micro cracks in Formula 1 Valves are detected with eddy current by EC-Works.
Benefits of ECT
Eddy current offers the following capabilities:
Quick, simple, and reliable inspection technique to detect surface and near-surface defects in conductive material Can be used to measure material electrical conductivity Measurement of nonconductive coating Hole inspection with the use of high-speed rotating scanner and surface probe.
Eddy Current Array Testing
Compared to single-channel eddy current technology, eddy current array
technology provides the following benefits: Drastically reduces inspection time. Covers a large area in one single pass. Reduces the complexity of mechanical and robotic scanning systems. Provides real-time cartography of the inspected region, facilitating data interpretation. Is well suited for complex part geometries. Improves reliability and probability of detection (POD).
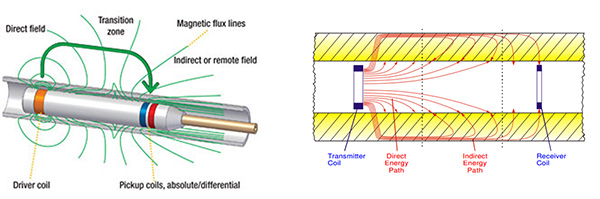
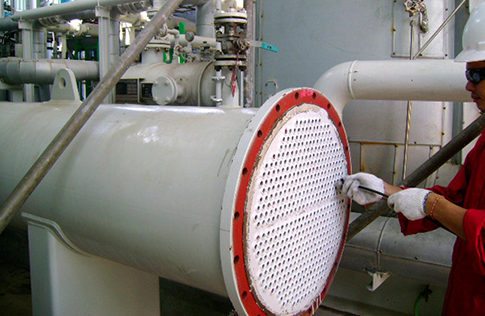
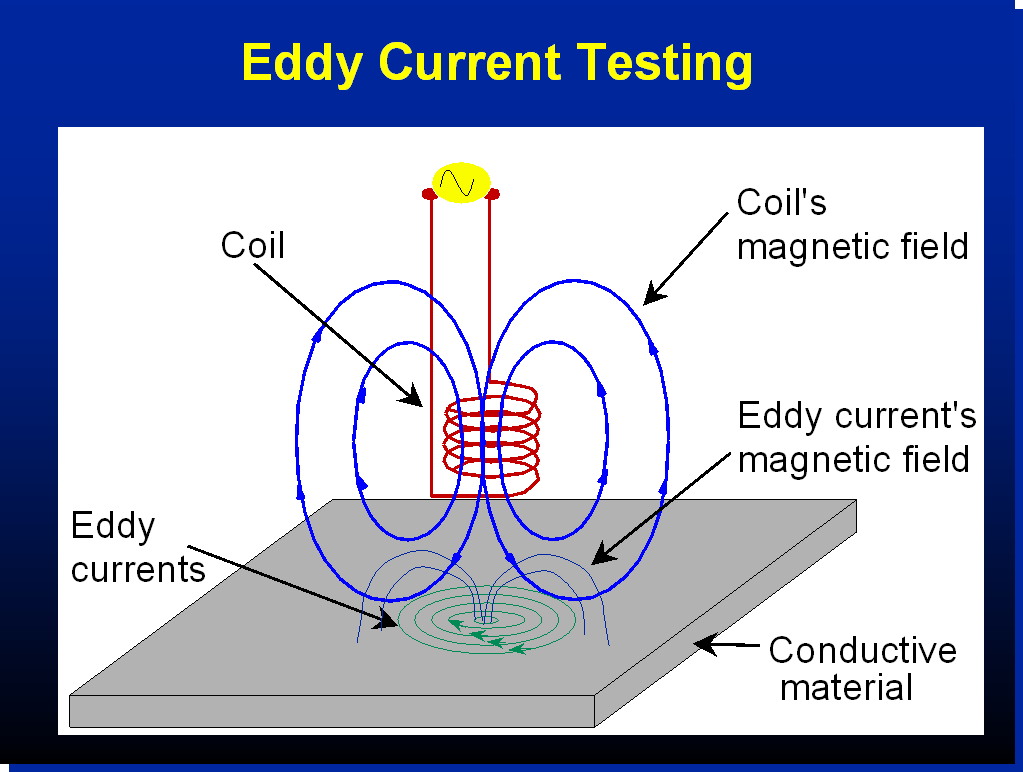
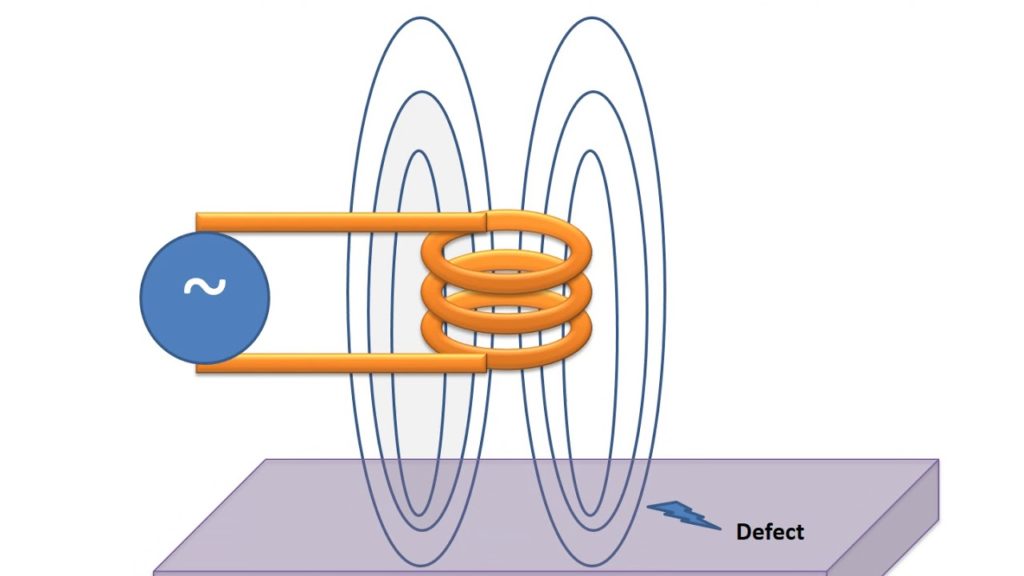